常用注塑件装饰工艺大全
塑料制品要成为一件广受消费者欢迎的产品,不仅要有一定的功能性,还要有炫丽的与众不同的外表,有些时候还需要将企业产品信息与品牌信息通过图文方式进行传达,这就需要对产品进行装饰。
注塑件装饰按装饰所处的加工工序段不同,大致可以分为四类:
注塑过程中直接加工类,主要运用材料、模具、注塑机等对制品外观进行加工;
注塑过程中间接加工类,主要是模内覆合加工,如模内注塑IMD、IML、IMR工艺等;
注塑成型后直接表面加工类,即直接在制品表面涂覆、印刷等,如喷涂、镀膜、数码印刷等;
注塑成型后间接加工类,借助一些载体如膜片等将已经做好的图案加工到制品表面,如转印、披覆等。
表 常见注塑件装饰工艺
(一)注塑过程中同步加工 |
(二)注塑成型后加工类 |
||
1、直接加工类——运用材料、模具、注塑机
|
混色 蚀纹 多色 速变模温 ...... |
1.直接表面加工类 |
喷涂 丝印 镀膜(水电镀、真空镀) 数码印刷(镭射雕刻、喷墨) ...... |
2、间接加工类——模内覆合加工类
|
IMD IML IMR 模内涂布 模外涂布 ...... |
2.间接加工类——运用载体 |
转印(移印、水转印、热升华/气染、热转印、压盖披复转印等)
披覆(贴纸、水贴纸、热贴、压差披覆复合等) |
下面我们来具体了解下这些常用注塑件装饰工艺。
注塑中同步加工类
直接加工类——运用材料、模具、注塑机
1. 混色(材料、高光)
双(多)物料在注塑机配置下,可以注塑成云彩或多层次色彩的产品。
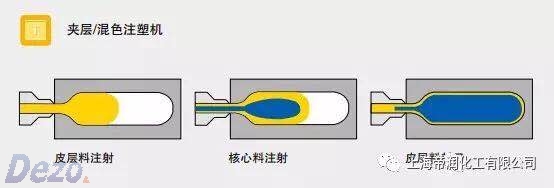
图 双混色注塑工作原理
2. 蚀纹(模具、抛光)
蚀纹工艺,香港称之为“晒纹”,台湾称之为“咬花”,“蚀纹”是书面语,英文名为texture 或texturing。
咬花是用化学药品如浓硫酸等对塑料成型模具内部进行腐蚀,形成蛇纹、蚀纹、犁地等形式的纹路,塑料通过模具成型后,表面具有相应纹路。与其他部分较大的差异是,咬花是对模具的加工,而其他部分则是直接对半成品加工。
咬花流程:洗模-粘模-化学检验-表面处理-印花处理-化学蚀刻-表面处理-QC-防锈处理-包装。
3. 多色(模具+设备、混)
多色多物料注塑制品是指两种或两种以上颜色的材料或不同材料通过一个或一个以上的流道注塑成型的塑胶制品。多色注塑制品由不同颜色的塑料材料通过注塑成型,每种材料在成型过程中不允许相互渗透,必须要严格区分开来,比如各种带标识的按键及汽车车灯等。
多色多物料注塑机由两个或两个以上注塑单元组成,根据注塑单元(副射台)的布置方式,可以分类为V型、L型、P型及W型。这几种类型的多色多物料注塑机各有特点,用户需要根据自身需求来选择。其中,V型及L型在欧洲注塑机的应用较为广泛,而日本及国产机台则多数采用P型。
4. 速变模温(模具+设备)
模具温度是注塑成型过程中影响制品质量的重要工艺参数。收缩变形是影响注塑制品最终尺寸精度的关键因素之一。
快变模温技术通过对模温的动态控制,可以有效提高熔体充模流动能力,降低注射压力,改善制品成型工艺;降低注射速率和熔体充模过程中受到的剪切力,减小最终制品的残余应力和翘曲变形,改善制品结构性能。模温的动态变化有效地避免熔体在型腔壁处形成冷凝层,消除制品表面的熔接痕、浮纤等缺陷,使制品表面呈现高光效果。
间接加工类——模内覆合加工类
IMD注塑制程就是将已印刷冲型好的装饰薄膜片材放入注塑模内,然后将树脂注射在成型片材的背面油墨层,使树脂与薄膜片材接合成一体固化成型的技术。
IMD制程包含IML、IMF和IMR。
1. IML
IML( In molding label):表面是一层硬化的透明薄膜(片材PE或PC),中间是印刷图案层,背面是塑胶层,油墨夹在中间,耐刮擦,不易褪色。
2. IMR
IMR( In molding roller),模内转印:将图案印刷在薄膜上,通过送膜机将膜片与塑模型腔贴合进行注塑,然后油墨层与薄膜分离而留在塑件上。在最终的产品表面是没有一层
透明的保护膜,膜片只是生产过程中的一个载体。
制程步骤:将薄膜送进模具內并定位,接着合模后图样转印至射出产品,打开模具后薄膜剥离,产品顶出。
技术特点:生产速度快、良率稳定、成本低,符合3C产业需求变化大、生命周期短的需求。
应用产品:手机、数码相机及3C产品等。
3. 模内涂布
模内涂层运用于BMC和SMC产品,首先将涂料粉末静电喷撒在加温的模具内,然后将BMC或SMC放入模具,合模后涂料粉末融化,在制品上形成涂层。因此制品形成,涂层也同步形成,此为模内涂层。
模内涂层是在模塑料加工同时,于模具内同步形成。可以遮盖和弥补制品表面缺陷,涂层美观坚实,具有杰出的耐刮擦和耐频繁摩擦性能,属环保性材料,使用中无有毒气体释放,可以显著地节约能源。
4. 模外涂布
与模内涂层不同,传统的涂层需要在BMC或SMC制品加工完毕,在离开模具以后进行烤漆或涂漆,称为模外涂层。
模外涂层是在模塑料经过热加工完毕后才可以烤漆或涂漆,这需要单独的烤漆生产线,制品上漆前必须清洗,然后经过喷漆和固化程序。这个烤漆工序有时由模塑料加工工厂自己完成,但更多的是委托专业烤漆工厂。烤漆线需要大量设备投资,较多人力投入,高耗电(清洗,压缩空气和热固化需要大量电力),且由于容易释放出对环境有害的有机气体,必须严格控制油漆气体污染环境。同时烤漆层耐刮擦和频繁摩擦性能不好。
注塑成型后加工类
直接表面加工类
1. 喷涂
喷涂是利用喷枪等喷射工具把涂料雾化后,喷射在被涂工件上的涂装方法。
工艺流程:注塑一底漆一烘干→面漆一烘干
优点:
-
颜色丰富;
-
液体环境中加加工,可实现复杂结构的表面处理
-
工艺成熟、可量
-
有独特的透明度,光泽度高
缺点:
-
成本过高,低成本定位产品不适用于此工艺
-
工艺相对复杂,良率较低。
2. 丝印
丝印是指把带有图像或图案的模版被附着在丝网上进行印刷,当承印物直接放在带有模版的丝网下面时,丝网印刷油墨或涂料在刮墨刀的挤压下穿过丝网中间的网孔,印刷到承印物上,通常丝网由尼龙、聚酯、丝绸或金属网制作而成。
丝网印刷设备简单、操作方便,印刷、制版简易且成本低廉,适应性强,适用于平面、单曲面或者曲面落差比较小的产品。
3. 镀膜类
电镀是金属电沉积技术技术之一,是一种用电化学在工件表面获得金属沉积层的金属覆层工艺。可以改变固体材料的外观,改变表面特性,使材料耐腐蚀、耐磨,具有装饰性和电、磁、光学性能。
1)水电镀
一般适用于ABS料、ABS+PC料的产品。主要工艺是将需电镀的产品放入化学电镀液中进行电镀。
水电镀法主要应用于打造高反射镜效果、增加附着层等,其优点是可镀大面积,成本低,缺点是电解液毒性高,工业污染大。

2)真空电镀
又称真空镀膜,是一种物理沉积现象,即在真空状态下注入氩气,氩气撞击靶材,靶材分离成分子被导电的货品吸附形成一层均匀光滑的仿金属表面层。一般适用范围较广,如ABS料、ABS+PC料、PC料的产品。因其工艺流程复杂、环境、设备要求高,单价比水电镀昂贵。
工艺流程:产品表面清洁、去静电--〉喷底漆--〉烘烤底漆--〉真空镀膜--〉喷面漆--〉烘烤面漆--〉包装。
4. 数码印刷类
1)镭射雕刻
镭雕:也叫激光雕刻或者激光打标,是一种用光学原理进行表面处理的工艺,与网印移印类似,通过镭雕可以在产品表面打字或者图案。
2)喷墨
喷墨印刷是一种非撞击的“点阵”打印技术,墨滴从小型机械中喷射而出,根据控制条件飞行记录在介质表面,直接在规定位置建立印刷图像。
间接加工类——运用载体
1. 转印类
1)移印
移印也叫曲面印刷,是先将油墨放入雕刻有文字或图案凹版内,随后将文字或图案复印到橡胶上,再利用橡胶将文字或图案转印至塑料成型品表面,最后通过热处理或紫外线光照射等方法使油墨固化。
2)水转印
水转印是利用水压将带彩色图案的转印纸/塑料膜进行高分子水解的一种印刷。
水转印以特殊化学处理的薄膜,经印上所需的色彩纹路后,平送于水的表面,利用水压的作用,将色彩纹路图案均匀地转印于产品表面,这时披覆膜则自动溶解于水,经清洗及烘干后,再上一层透明的保护涂层,这时产品已呈现出一种截然不同的视觉效果。
两种工艺流程:
-
制作水标转印花纸→花纸浸泡→图案转贴→干燥→成品
-
水披覆膜纸制作→被转印物喷底漆后烘干→膜纸入水→喷活化剂于膜上→物件触膜转印→水洗→烘干→喷光油带干后包装成品
3)热升华/气染
热升华是利用分散染料(油墨)的升华特性,通过基材载体,在一定温度、时间和压力的条件下,使分散染料转移到承印物中的一种装饰技术。热升华工艺早期在织物转印上非常普遍,随着其应用的推广近年在各种喷涂金属型材上的转印装饰木纹开始兴起,并备受家居装潢青睐。热升华(气染)工艺主要应用用于喷涂、烤漆、电泳等处理后的金属表面转印装饰。
4)热转印
热转印是将花纹或图案印刷到耐热性胶纸上,通过加热,加压,将油墨层的花纹图案印到成品材料上的一种技术。热转印颜色更为丰富,薄且不易开裂、不脱落。
5)压盖披复转印
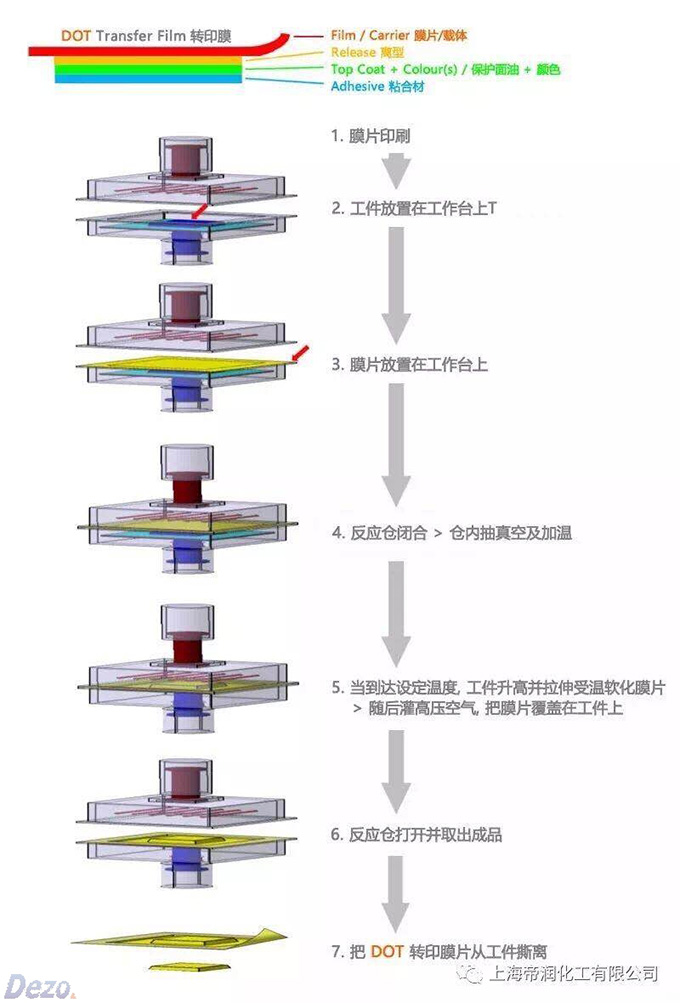
图DOT 压差披复转印工序说明,图片来自SPRINGFIELD CMF官网
2. 披覆
1)贴纸
是将印有花纹和图案的贴纸紧贴在产品上。
2)水贴纸
水贴纸又称水转印贴纸、水标、花纸、无膜标、水贴花纸、水转印、转印纸。水贴纸是一种全新的产品表面处理技术, 它是以水为介质, 结合尖端的柯式印刷及精密的丝网印刷技术在物体表面进行图案成型的崭新工艺。
3)热贴
热收缩膜标签是一种采用专用油墨印刷在塑料膜或塑料管上的薄膜标签.在贴标签的过程中,当加热时收缩标签便会很快地沿着容器的外轮收缩,紧贴在容器表面。
4)压差披覆复合
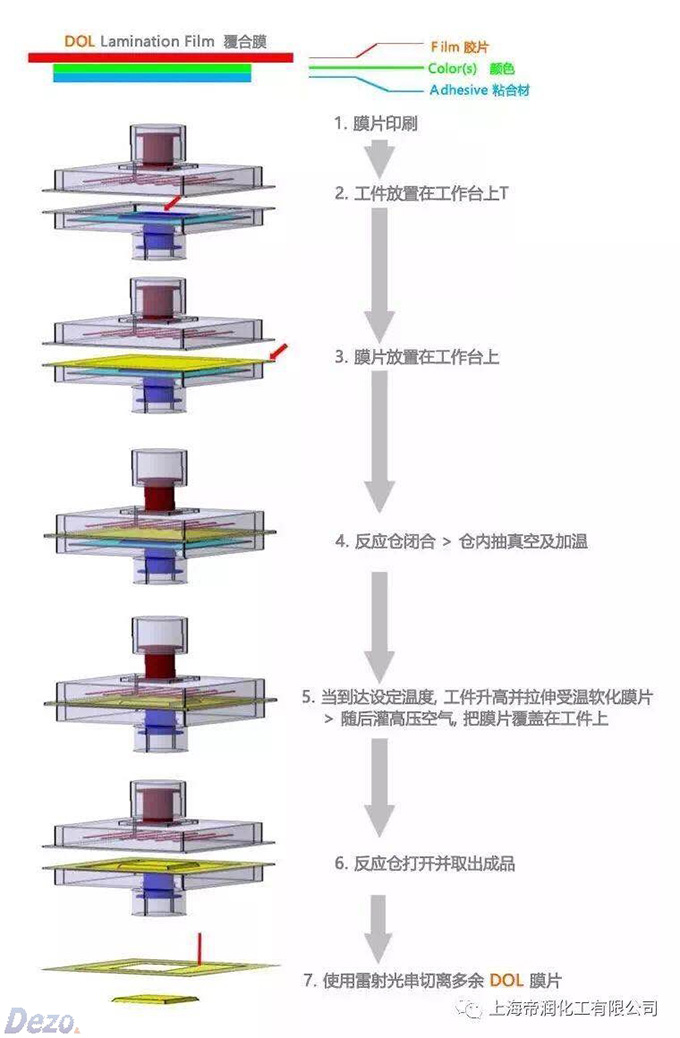
图 DOL 压差披覆复合工序说明,图片来自SPRINGFIELD CMF官网
公司:上海帝润化工有限公司,专业的 塑料润滑剂 供应商。技术咨询热线:021-52683036
- 上一篇:PVC与CPVC的差别在哪里? 2022/6/28
- 下一篇:塑料助剂大全 2022/6/28